
Five Maintenance Tips to Keep Your Titan Blast Cabinet Running at Peak Performance
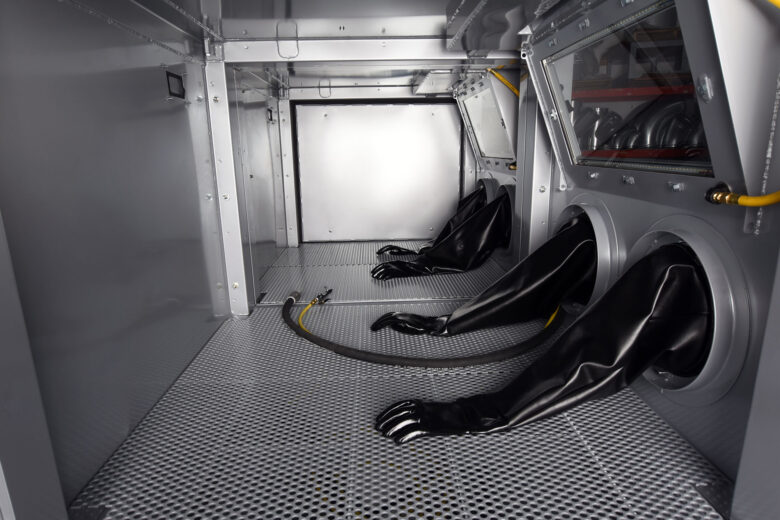
Due to the abrasive media and the high pressure at which it moves, blast equipment—especially nozzles and hoses—takes a beating. To maintain your blast cabinet’s high performance, and worker safety, Titan recommends these five maintenance tasks.
1. Replace worn nozzles often
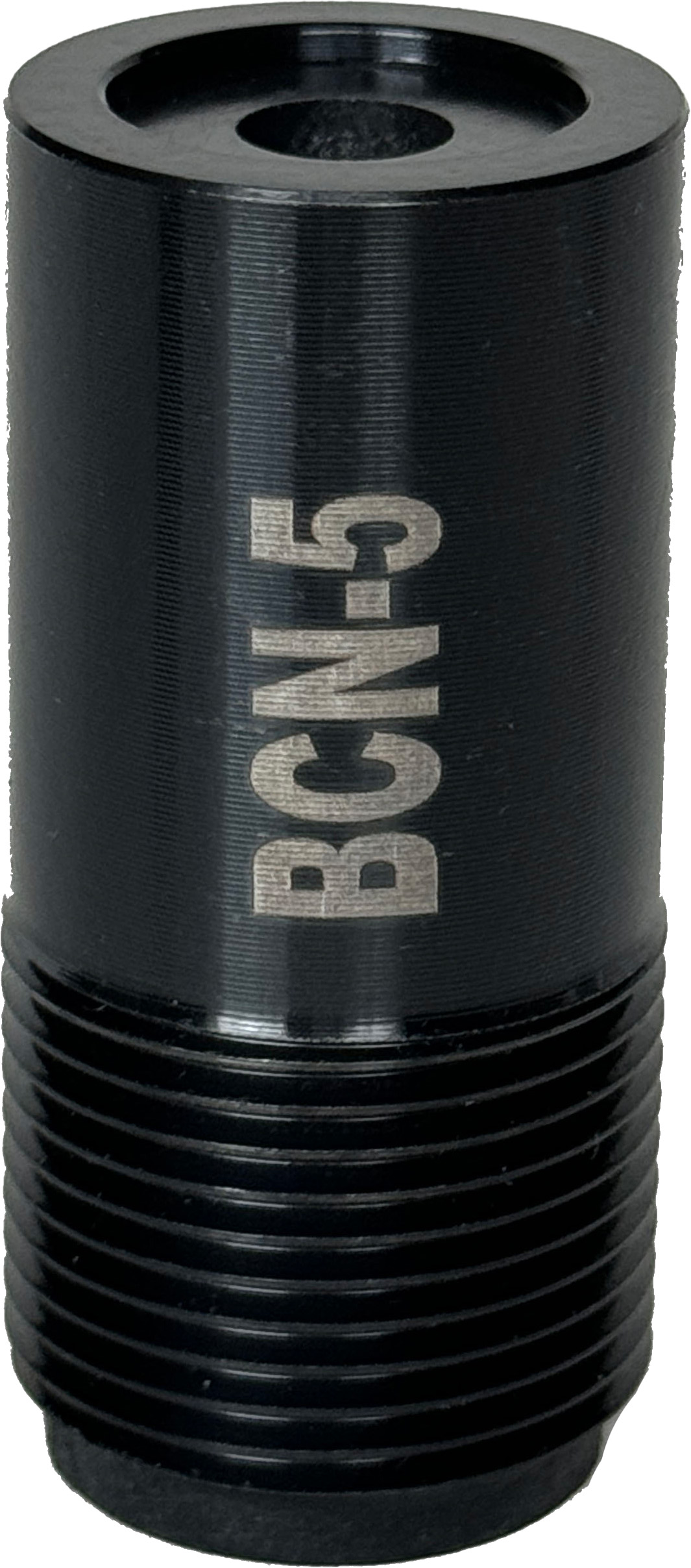
The blast nozzle consists of the outer jacket—typically made of steel, brass, polyurethane, or aluminum—and the inner liner. Liners are made from various materials, the most common being boron carbide, tungsten carbide, and silicon carbide.
Over time, the bore (hole diameter) becomes larger – which impacts performance. Media pressure is reduced, more media is expended, and the spray pattern changes. The larger the hole, the more air is required, and the more media is sprayed out – resulting in a costly waste of energy and material.
The service life of a nozzle depends on the liner material and the media used, while factors such as blast pressure, media size, and particle shape can further affect its lifespan.
Nozzle Material | Steel Shot/Grit | Expendable Abrasives | Aluminum Oxide |
---|---|---|---|
Boron Carbide | 1500 – 2500 | 750 – 1500 | 200 – 1000 |
Silicon Carbide | 600 – 1000 | 400 – 600 | 50 – 100 |
Tungsten Carbide | 500 – 800 | 300 – 400 | 20 – 40 |
Ceramic | 20 – 40 | 10 – 30 | 1 – 4 |
2. Use high quality nozzles
You can purchase imported nozzles from low-cost distributors, or you can buy American-made blast nozzles developed specifically for high-performance blasting. All Titan blast nozzles are made in the USA.
Each material type has its pros and cons:
- Boron Carbide nozzles are standard on all Titan blast cabinets, though we can provide any nozzle type you prefer. While boron carbide lasts longer, it is a more fragile material, meaning if you bang your nozzle around, you may break it.
- Silicon Carbide nozzles are an in-between nozzle. They last longer than tungsten carbide but are fragile like boron carbide, only slightly less expensive.
- Tungsten Carbide nozzles have a good service life, are more durable than boron or silicon carbide, and are less expensive.
- Ceramic nozzles are very inexpensive nozzles found on homeowner-grade equipment. They don’t last long (as you can see from the service life chart above) and can shatter when dropped – posing a safety hazard. Titan doesn’t recommend using these for blasting.
3. Check blast hoses regularly for wear
When the blast hose is straight, media rushes through it unimpeded. As the technician blasts parts inside the cabinet, the hose is bent to reach around the parts. When bent, the media bangs into the hose wall, creating wear spots at the outer edge of the bend. These wear spots can lead to holes and escaping media, compromising worker safety and reducing performance.
Always check your hoses for wear and replace them as needed.
4. Pulse clean dust collector filters
Titan dust collectors feature a reverse pulse cleaning system, which momentarily reverses the airflow through the filter element. This reversed air flow knocks the caked-on dust off of the filter and into the hopper or dust drum while the collector is in operation.
By performing the pulse cleaning regularly, you won’t have dust build-up on your Titan filter cartridges. It also means you don’t need to send them out for cleaning – saving you big bucks.
5. Add a rubber liner if using aggressive media
All Titan blast cabinets come as a complete system, including a 3 cu. ft pressure vessel, our Small Cartridge Dust Collector, and a Media Reclaim System.
As already stated, blasting takes a toll on your equipment – especially the cyclone in the media reclaimer. To prolong its life, we recommend adding a rubber liner, which Titan provides as a factory-installed option. Please inquire!
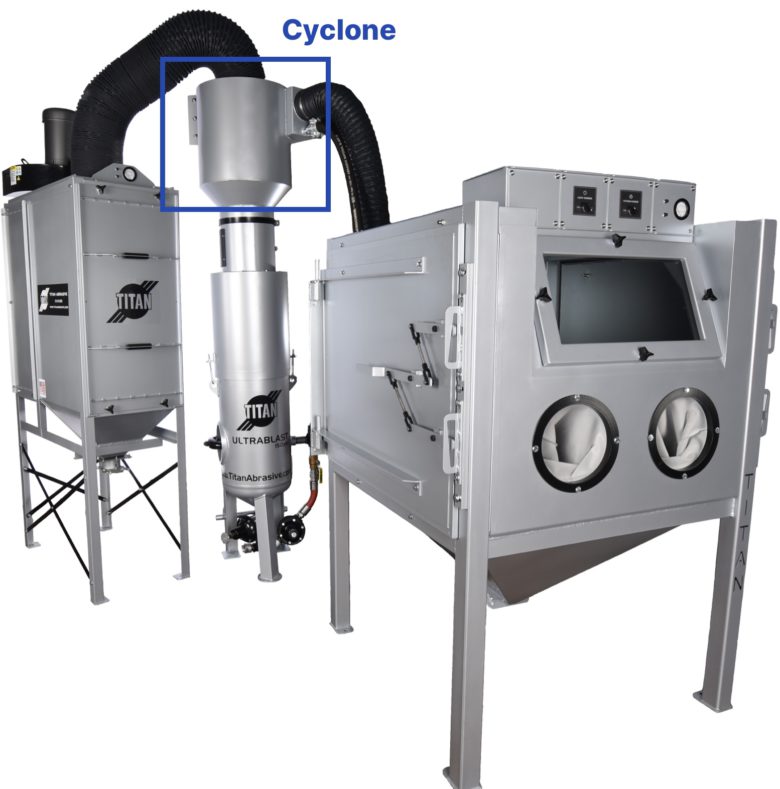
Transform your work with Titan blast cabinets
To learn more, complete the contact form below – or visit the Blast Cabinet product page.
Contact Us
"*" indicates required fields
Brandon Acker: President
Brandon purchased Titan Abrasive from his uncle and founder in 2013. Titan has since redesigned its entire product line to solve dozens of industry challenges.
Brandon purchased Titan Abrasive from his uncle and Titan founder, Bruce Maurer, in 2013 after spending five years learning the ins and outs of the business. He and VP of Engineering Brian Fox have completely redesigned the entire product line to solve the dozens of challenges that have plagued the blasting industry for decades.
Brandon is passionate about American manufacturing, the jobs it creates, the quality produced, and the bright future that lies ahead. He’s a frequent guest on manufacturing podcasts where he shares his deep industry expertise. Brandon holds a Bachelor of Science degree from Arizona State University.