
How Do We Compare Industrial Blast Cabinet Claims “Apples-to-Apples”?
A prospective customer called to inquire about our blast cabinets and wanted to know what made Titan’s different. He said many companies sell industrial blast cabinets, and as far as he could tell, they’re all the same.
If you’re in the market for a blast cabinet that can deliver high-performance blasting on a daily basis, and you want to compare apples-to-apples, then this FAQ is for you.
You’ll learn the difference between blast cabinets designed for heavy-duty industrial applications – which is what Titan manufactures and sells – and those designed for small shops and DIYers.
What exactly is an “industrial” blast cabinet?
“Industrial” is often applied to all types of blast cabinets, including lower-end brands designed for occasional blasting in a home workshop or an auto repair shop.
These “industrial” models are good for blasting low-volume parts, but they’re definitely not suitable for high production industrial applications that require multiple work shifts.
Titan blast cabinets, on the other hand, are designed for these high production environments.
To visualize the difference, think Toyota Rav4 versus a Ford F-Series. You can use either vehicle to transport items, but if you’re doing heavy construction work day in and day out, the Ford truck is your vehicle of choice.
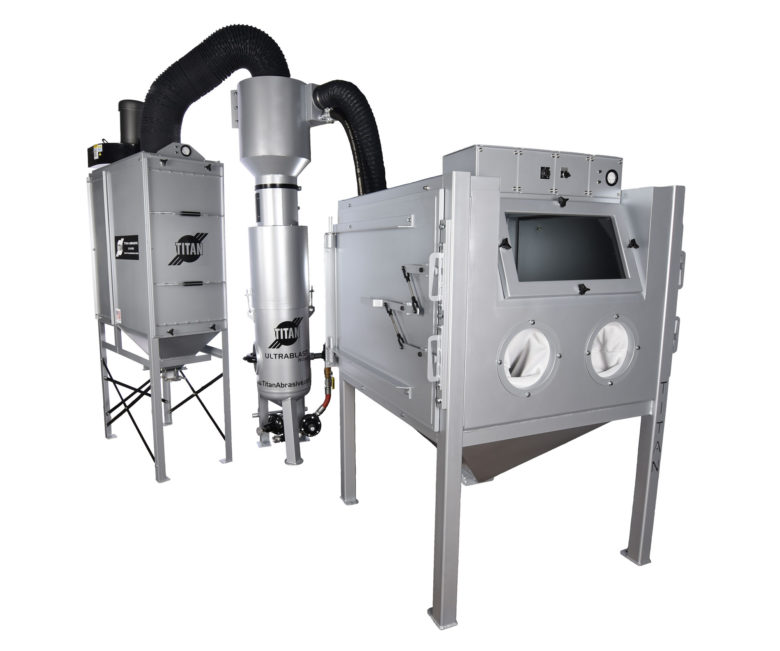
What should we look for with regard to how a blast cabinet is constructed?
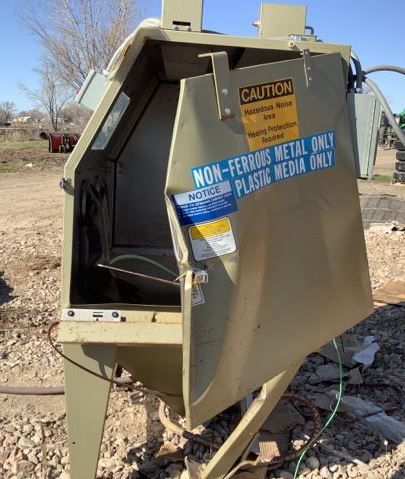
Look for blast cabinets that incorporate a structural steel, welded frame versus a sheet metal frame.
Sheet metal, by its very nature, is malleable – which means it doesn’t hold up well to years of industrial shop floor abuse. It also crumples like paper when a forklift hits it.
Structural steel, on the other hand, is very strong and won’t bend or crumple. We made the Titan blast cabinet frame strong enough to withstand the normal bumps and bashes from distracted forklift drivers.
Read: Titan Blast Cabinet – Built to Withstand Years of Abuse
We need a leak-proof cabinet. How do we evaluate the various claims in the market?
Leaks are most likely going to come from around the door seals. Don’t be swayed by companies who state a welded frame prevents leaks or that welding eliminates seams – and thus leaks – around the blast cabinet frame. That claim is bunk.
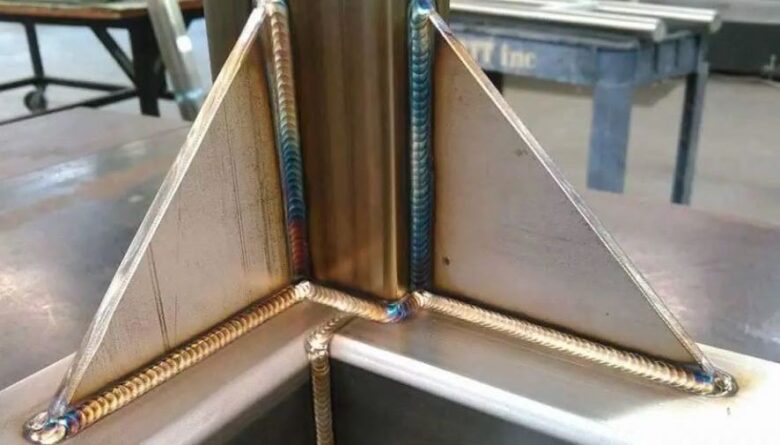
Fact #1: In order to join two pieces of steel, you have to weld them, which creates a seam. This is true whether the weld is created by hand or by automation.
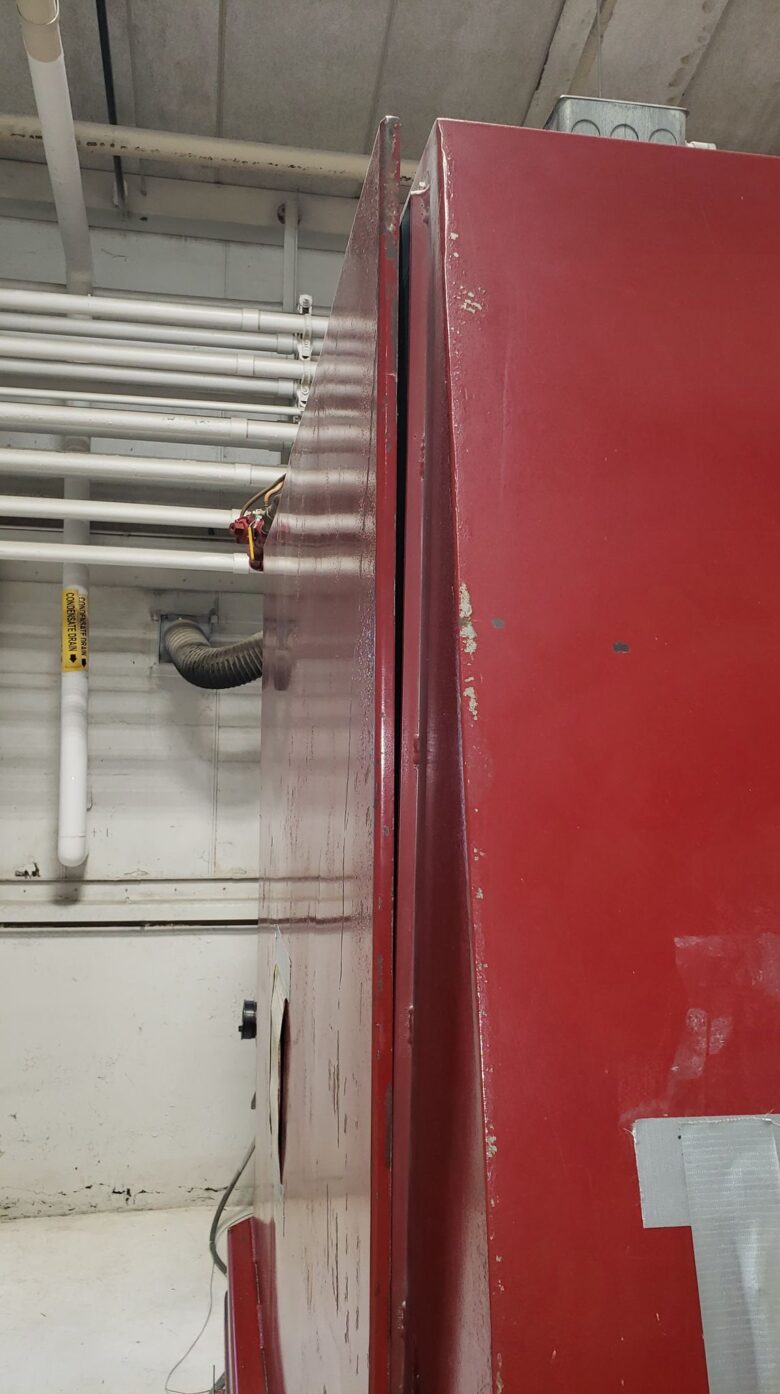
Fact #2: The reason most blast cabinets leak is due to warped or bent doors.
Most of the decent blast cabinets on the market incorporate double panel doors – and the companies claim these doors won’t warp or bend.
The fact is, they do warp and bend. One reason is because of the single latch locking mechanism. The locking point, located in the middle of the door panel, causes the door to bow out above and below the locking mechanism. Over time, the door leaks.
Titan solved this problem by designing our blast cabinet doors with self-adjusting dual door latches that lock at two points, rigid steel channel, multiple points of adjustment, and double panels with a knife-edge that presses into the door gasket to create a perfect seal.
Read: Challenge Solved! Titan Blast Cabinet Doors Will Not Leak or Warp. Guaranteed.
How do we evaluate performance? Should we go with suction or pressure?
For heavy-duty industrial applications on the shop or factory floor, you want a pressure blast cabinet.
Why? Because they’re 5x the speed of a suction cabinet. Don’t settle for less or you’ll be in the market for a new, high-performance blast cabinet within six months.
How important is visibility and what should we look for?
Visibility inside the blast cabinet is determined by two factors: dust collection and lighting.
Dust collection
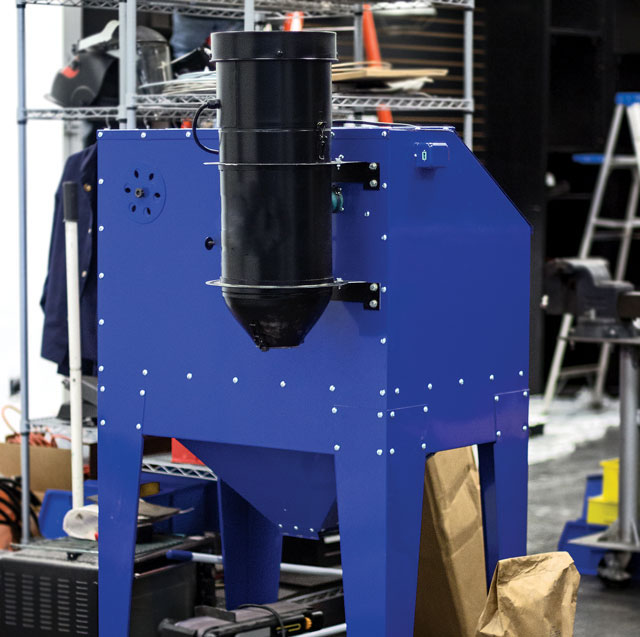
Some blast cabinets billed as “industrial” use a canister dust collector or a filter bag – a very low-end and potentially messy solution, especially when changing out the dust bags.
For industrial applications, your blast cabinet should have a cartridge dust collector with a minimum of 600 CFM (depending on cabinet size). Titan blast cabinets come standard with our Small Cartridge Dust Collector featuring Nanofiber Filtration.
Read: Titan’s Modular Dust Collectors
Lighting
Traditional blast cabinets use fluorescent tubes or halogen flood lamps placed into the cabinet ceiling. The problem with either type of lighting is safety (potential for broken bulbs and toxic chemicals let into the environment) and energy inefficiency.
All Titan blast cabinets feature our patented LED lighting incorporated into the window frame to deliver improved safety, no shadows, and 6,600 lumens of light output. This means they’re bright!
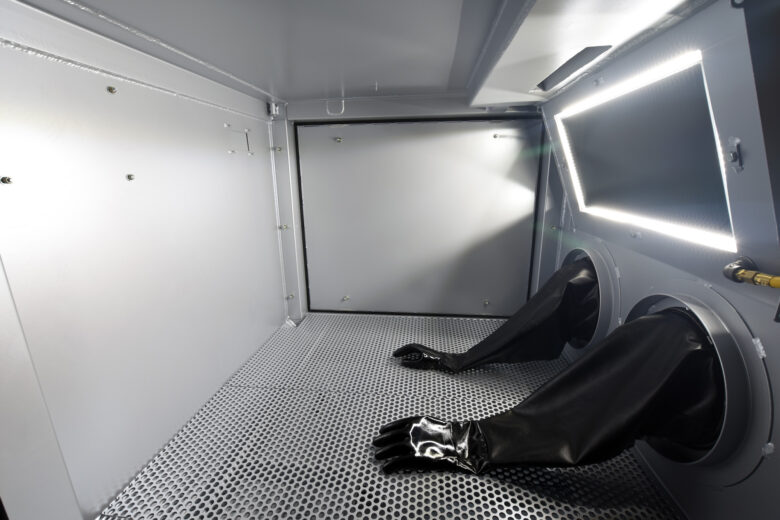
Do you have a downloadable chart to help us compare blast cabinet features?
You can download the short version of this FAQ as a PDF and use the chart below to compare features as you research industrial blast cabinets.
Blast Cabinet Feature | Titan | Other Brands |
---|---|---|
Structural Steel Frame, including legs | ||
Double-Panel, Leak-Proof Doors with channel frame, knife edge, and dual, adjustable locking mechanisms | ||
Lift-off door hinges for easy removal and customization | ||
Patented LED Window Frame Light; 6,600 Lumens | ||
Proximity Sensors – Detects if blast cabinet doors aren’t shut properly | ||
Bolt-in Floor Supports – for easy replacement of cabinet floor | ||
100% Electric Controls | ||
Customizable Control Panel | ||
Easy-Change Gloves – Removable from outside the cabinet | ||
Moveable Foot Pedal | ||
Removable Lifting Bars | ||
Complete System — Made in USA: Energy Efficient, Cartridge Dust Collector Media Reclaim System 3-cubic foot pressure vessel | ||
Standard Features: 3-cubic foot pressure vessel 12-gauge all-welded steel construction Heavy-duty cast iron valves that don’t clog Tungsten carbide blast nozzle Pressure regulator and moisture separator Blow-off gun 3/16” perforated reinforced floor | ||
Built for manufacturers and industrial job shops requiring heavy-duty, high-performance use |
Brandon Acker: President
Brandon purchased Titan Abrasive from his uncle and founder in 2013. Titan has since redesigned its entire product line to solve dozens of industry challenges.
Brandon purchased Titan Abrasive from his uncle and Titan founder, Bruce Maurer, in 2013 after spending five years learning the ins and outs of the business. He and VP of Engineering Brian Fox have completely redesigned the entire product line to solve the dozens of challenges that have plagued the blasting industry for decades.
Brandon is passionate about American manufacturing, the jobs it creates, the quality produced, and the bright future that lies ahead. He’s a frequent guest on manufacturing podcasts where he shares his deep industry expertise. Brandon holds a Bachelor of Science degree from Arizona State University.