Custom Blast Rooms
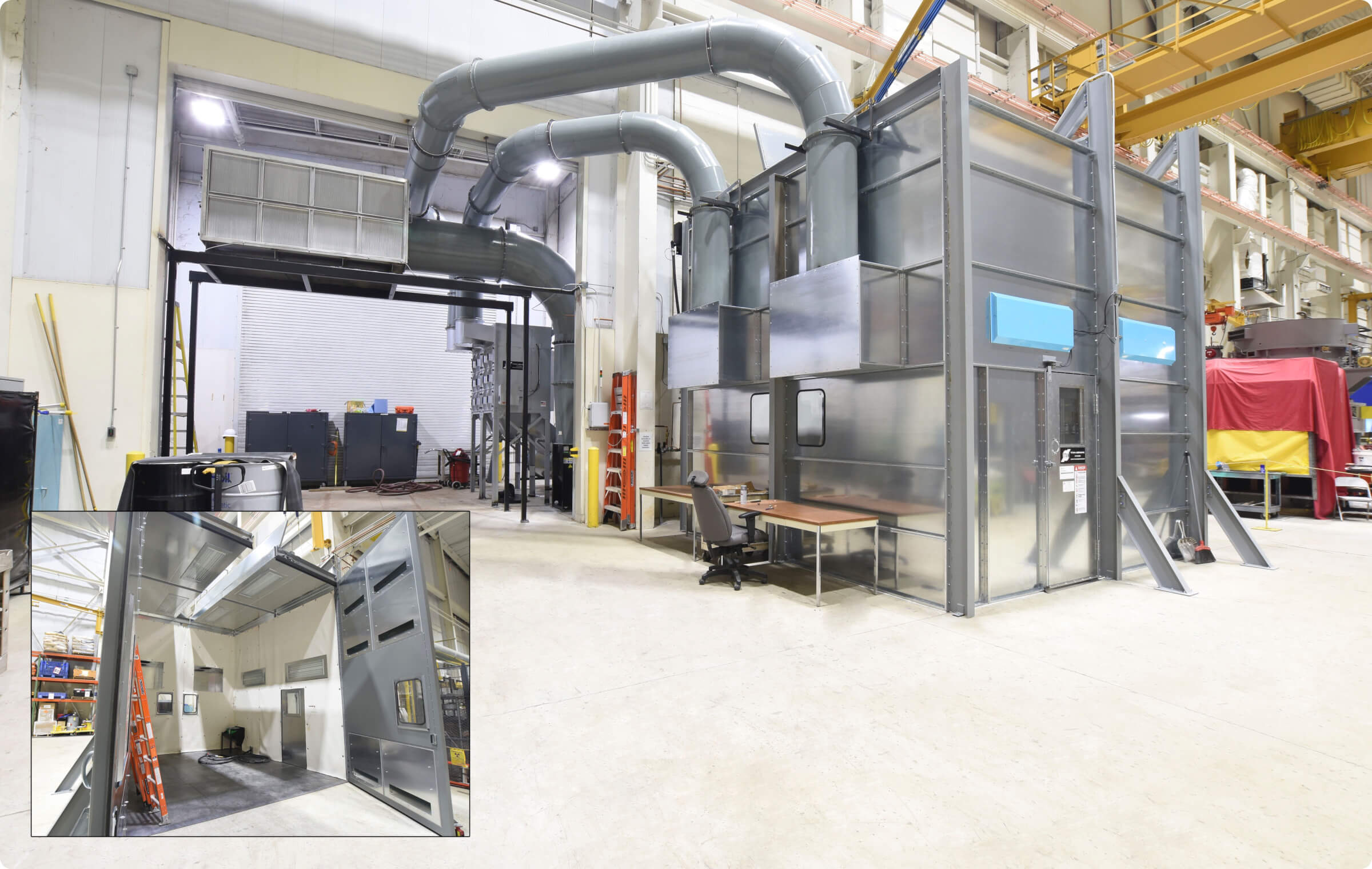
The Complete Titan Blast Room System
Custom-engineered Enclosure
Media Reclaim System
Cartridge Dust Collector
Blast Machine
Control Panel
Ductwork
Explore the Components
Custom-Engineered Enclosure
- Complies with all Federal, OSHA, and NFPA regulations
- Custom engineered to your requirements, part size, floor space, ceiling height, access, etc.
- Easy to assemble flanged bolt-together galvanized steel panels, available in 14-gauge or an optional 11-gauge
- I-beam support structure for maximum durability and safety
- Rear access, six tube, 48-inch LED blast lights with a Lexan polycarbonate lens
- 14-gauge galvanized steel panels
- Baffled air inlet louvers
- Blast shields for intake and exhaust vents to prevent media from exiting the enclosure
- Safety door limit switches which stop the blasting operation when booth doors are opened
- Swing-type or bi-fold doors
- Personnel door
Optional Upgrades
- 11-gauge galvanized steel panels for heavy-duty applications
- White rubber lining to protect walls, reduce noise, and provide a brighter work environment
- Rubber roll-up doors
- Crane slots
- Pass-through doors (doors on both ends of the enclosure)
- 3-axis man lifts
Media Reclaim System
- Customized to your application and desired abrasive
- Two styles:
- Mechanical – Bucket Elevator
- Air-wash separators, vibrating screens or rotary drum, to clean and classify media
- For high-production environments
- Pneumatic – Vacuum
- Cyclone separator recovers usable media; dust and broken-down media is drawn out by dust collector
- For lightweight media
- Mechanical – Bucket Elevator
Optional Upgrades
- Full or Partial Media Recovery Screw Floors – available as Single Screw, H-Shape, U-Shape, or Full Floor
- Rubber-lined cyclone for aggressive abrasives, such as aluminum oxide
Cartridge Dust Collector
- Titan Cartridge Dust Collectors are sized to fit each individual room according to room size, parts being blasted, amount of dust from the blast media, and airflow required for the abrasive media cleaner.
- Captures dust-filled air, filters it, and returns the clean air to the plant.
- Delivers maximum efficiency and rugged durability.
- Requires zero outside venting of air.
- Eliminates heated and cooled air loss — significantly reducing energy costs.
- Internal abrasive wear inlets — bolt-in and replaceable
- Smaller footprint and overall height than the leading competition
Optional Upgrades
- Sizes start at 600 cfm and go as high as needed
- Photohelic Gauge – Provides fully automated cleaning, longer filter life, reduced air consumption – factory installed
- Shorter Legs – For low ceiling height conditions
- Hopper Butterfly Valve Assembly – Upgrade to standard slide gate
- External Abrasive Wear Inlet
- Hazardous Condition Controls
- Explosion Venting
Blast Machine
- 6 cubic foot blast machine
- Pressure-hold remote control system
- 24VDC low voltage controls for blast room applications
- Heavy duty cast iron valves
- 50’ blast hose with couplings
- Blast nozzle
Optional Upgrades
- Multiple blast operators – Larger capacity blast machine (10 cu ft)
- Multiple blast machines
- Large capacity media storage hoppers
- Remote blow down switch for easy refilling without leaving the blast room
Control Panel
- Single-point connection (available in 208, 230 or 460 volt 3-phase)
- NEMA-rated enclosure
- Magnetic motor starters
- Start/Stop buttons for motor starters
- Fused disconnects
- Light switch
- Safety door interlocks with delay timer
- System operating lights
- Door mount disconnect switch
- 24VDC power supply for blast system
Optional Upgrades
- Variable frequency drives (VFD)
- PLC-based control system with touchscreen
Ductwork
- Designed for the location and application
- Long-radius elbows for optimal airflow
- 12 gauge, galvanized steel, seam welded
- Clamp together with adjustable sleeves for maximum versatility and easy installation
- Heavy duty steel withstands high velocity abrasive media dust
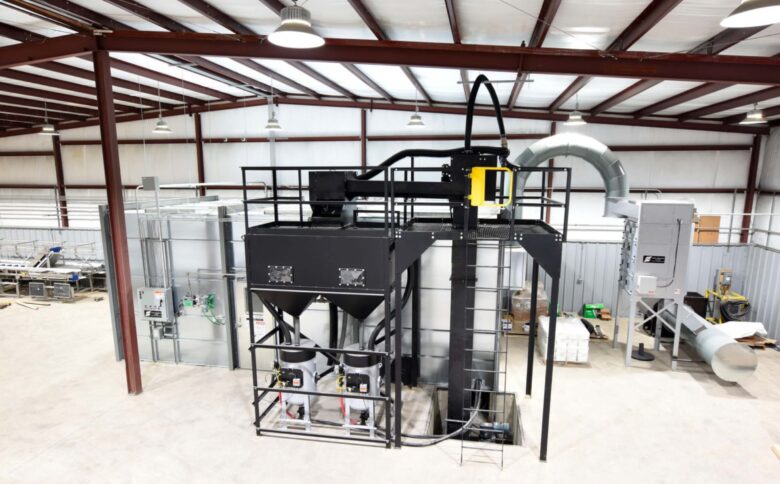