
Have a Complex Blast Room Challenge? Titan Can Solve It
One of the benefits of buying your blast room and other components from Titan Abrasive is that we can customize your system to suit your specific application or work environment.
In this piece, we detail five of the more complex customizations we’ve done for customers. Each customer had a specific requirement, which meant incorporating our engineering know-how, product and industry knowledge, and creative problem-solving.
Read through each case study and if you have a complex blast room challenge, call us. We can definitely work with you to provide a customized blast room system – on time and on budget.
Customer: U.S. Army
Application: A 20’W x 16’H x 55’L blast room and matching-sized paint booth installed end-to-end with drive-through capabilities
Constraint: Could only buy from a single source
Solution: Titan provided both the blast room and paint booth
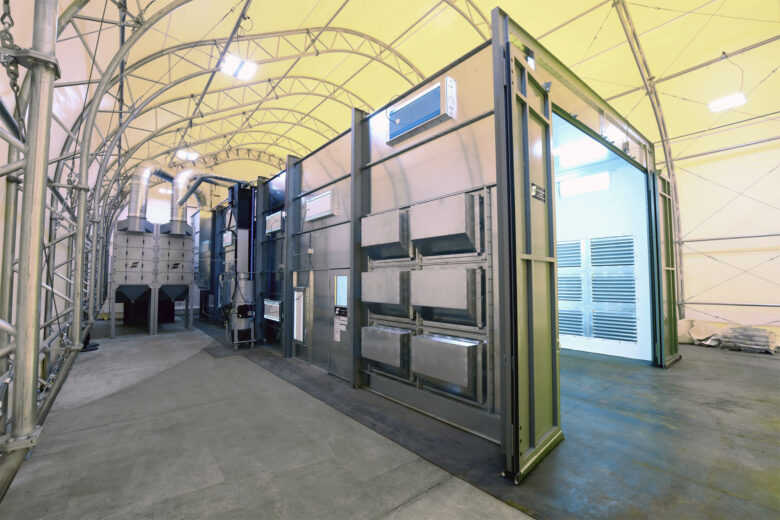
Customer: GE Aerospace
Application: A large blast room for blasting jet engine components
Constraint: The customer required the use of virgin blast media and disposal of the spent media into super sacks. This meant they had to use new blast media on every component and dispose of the spent media immediately after blasting. Due to the large size and volume of components, blasting would generate a lot of spent media.
Solution: Titan chose to source a large industrial vacuum system rather than use one of our own recovery systems. This gave us the upper hand over the competition as most manufacturers only want to sell what they manufacture.
Here at Titan, our priority is to design the absolute best systems for customers’ needs – even if it means sourcing components from other manufacturers.
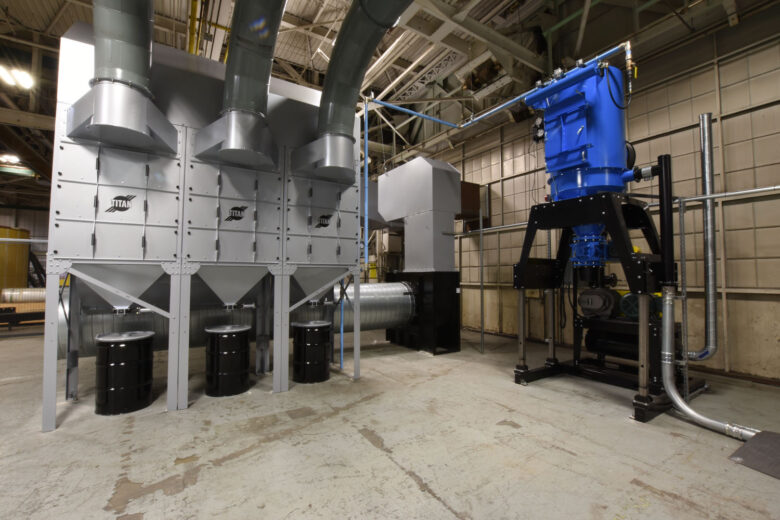
Customers: SeaCast & Ethos Energy
Application: Separate blast rooms and media for different components – for two different companies
Constraint: Both customers (two different companies) had the same exact challenge: due to cross-contamination issues, each one required separate blast rooms and recovery systems – and each had a tight budget.
Solution: In order to meet each customer’s budget, Titan designed two blast rooms with separate media recovery systems that could use a single dust collection system. To accomplish this, we designed and installed blast gates in the ducting coming off each recovery system to the dust collector.
We also took this approach one step further. In order to eliminate the possibility of operator error, we automated the blast gates via a single A/B selector switch on the control panel. The switch allowed the operator to simply select which blast room he would be working in.
Once selected, the blast gates automatically set to that room, closing off the other room and eliminating the possibility of closing both systems and dead-heading the dust collector.
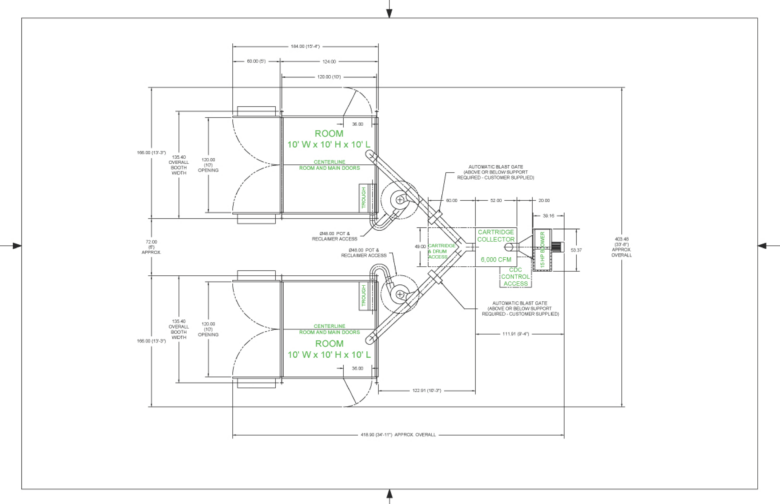
Customer: Summit Metal Fabricators
Application: Dual media reclaim systems
Constraint: Similar to the SeaCast and Ethos Energy systems, Summit Metal Fabricators required two separate media recovery systems. However, they wanted to use them in the same blast room.
Solution: Titan designed custom ductwork with manual butterfly valves to control which recovery system was in use at any one time.
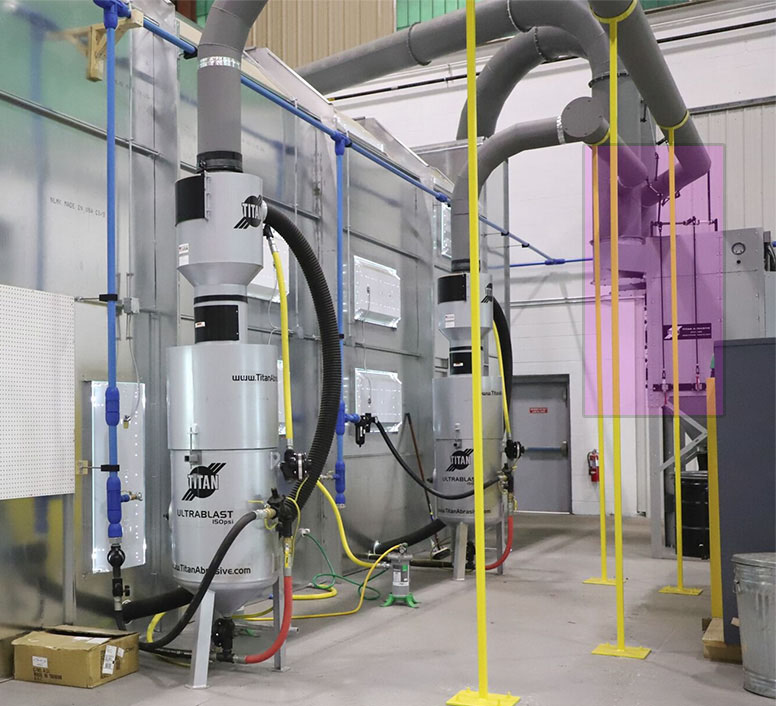
Customer: Painters Union
Application: A dual operator system for a training center
Constraint: The customer had a very small budget but needed a dual operator system with two separate blast machines. Typically, this can be a very pricey system.
Solution: Titan designed a custom diverter valve using our above-ground mechanical recovery system to allow the use of two separate blast machines. The diverter valve allowed the recycled media to be sent to either blast machine separately or split between the two.
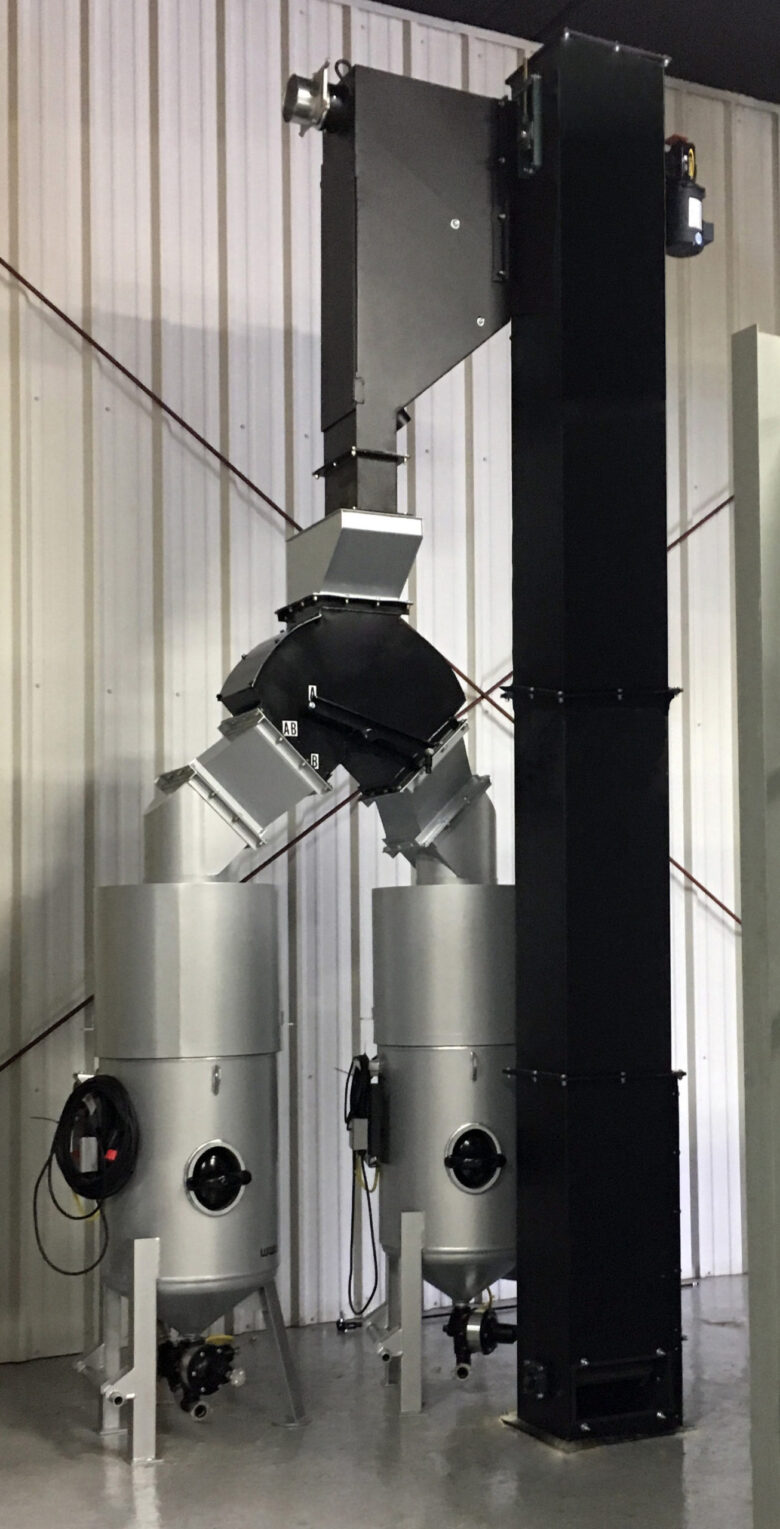
Brandon Acker: President
Brandon purchased Titan Abrasive from his uncle and founder in 2013. Titan has since redesigned its entire product line to solve dozens of industry challenges.
Brandon purchased Titan Abrasive from his uncle and Titan founder, Bruce Maurer, in 2013 after spending five years learning the ins and outs of the business. He and VP of Engineering Brian Fox have completely redesigned the entire product line to solve the dozens of challenges that have plagued the blasting industry for decades.
Brandon is passionate about American manufacturing, the jobs it creates, the quality produced, and the bright future that lies ahead. He’s a frequent guest on manufacturing podcasts where he shares his deep industry expertise. Brandon holds a Bachelor of Science degree from Arizona State University.